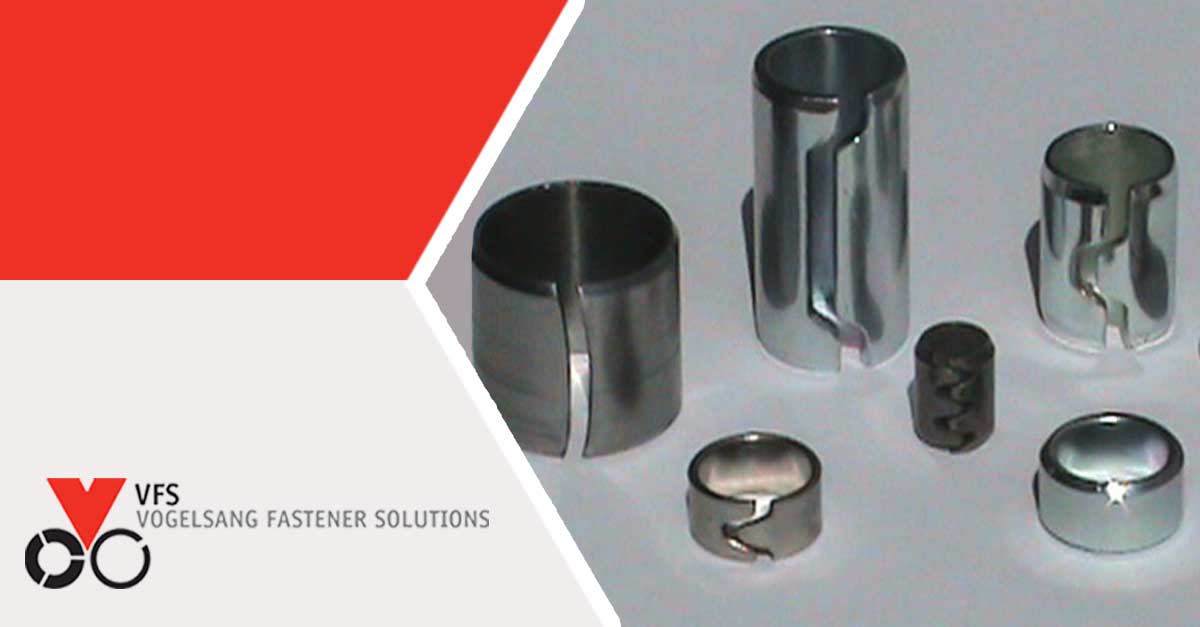
As automobile manufactures’ priorities focus more and more on cost savings and fuel efficiency, compression limiters are proving an invaluable component in the application stack. The drive for reduced weight in vehicles and the growth in plastics and plastic production has set compression limiters up as the go-to fastener of choice.
These non-threaded inserts are designed to protect plastic and rubber parts from loads created by the tightening of bolts. Learn more about some of the features of compression limiters that make them such a key component in automotive and trucking industries.
Why Compression Limiters?
In order to reduce weight and improve fuel efficiency in vehicles, metal components are commonly being swapped out for plastic. But these lighter components must still be bolted to something solid to stop the plastics from being crushed, cracked or split.
Everywhere a plastic component is fixed into or onto a vehicle by means of fasteners such as bolts or screws, whether in an airbag assembly box, electronic module, bumper, fuel pedal assembly, oil pan, manifold, water pump, or valve cover to name a few, there is a risk of damaging or destroying the plastic. The normal forces of fasteners in a tightened state can exceed the permissible surface pressure of plastic, resulting in immediate damage, or in breakage over time that can cause catastrophic failure.
As plastic components have become vastly more prevalent in manufacturing, an additional solution is required. Compression limiters are the protective metal component that supports weight reduction and prevents these plastic parts from being cracked and crushed.
Multiple Designs, Myriad Benefits
Compression limiters are non-threaded inserts produced with multiple design features in various shapes and materials that can be combined to afford you overall cost savings and help maintain the integrity of your application.
They can be made using one of two specific designs: either with an open seam that is inserted after molding, or with a closed seam that you can mold around without risk of plastic material seeping into the center of the pin.
Open seam limiters, also known as insertion parts, gap seam bushings, or split seam limiters, are inserted into an application where the plastic mold is already complete. They are designed to compress on insertion, then return to their original dimensions, creating tension against the inner wall of the component to hold it in place. The gap in the split seam will provide radial tension to ensure that the limiter does not fall out before final installation of primary components.
This design uses tension to maintain contact with the plastic component, preventing it from becoming dislodged. When an open seam compression limiter is inserted into a mold, it acts similarly to a tension pin, and as such, offers an affordable alternative to tubular or machined parts.
Closed seam limiters, also referred to as injection molded parts or “butt seam” bushings, are designed to be inserted into the mold prior to the plastic being injected. When molten plastic is molded around a compression limiter, the closed seam prevents the plastic from entering the center of the component. When the plastic cools, the limiter is permanently molded into the assembly and will not separate from its host.
We can even design a seam that does not allow seepage and the open end of the seam acts as an anti-rotation feature.
These special fasteners and their unique designs offer substantial cost and weight savings over solid limiters.
Special Features For Even More Benefits
Our compression limiters can be designed to any specification of varied sizes in diameters and lengths, and can include unique slot shapes such as wavy, offset or straight. They can also include additional features including grooves, knurling, flanges, internal and external chamfers, slots closed on the inside/outside, or both, and protrusions.
Knurled compression limiters are particularly beneficial in automotive and trucking, as the knurls offer additional gripping tension that reduces the risk of spin or of a part becoming dislodged.
Enclosed slot edges are available on request, and offer a distinct advantage. The edges are on the transition from the bevel to the slot below the surrounding diameter so that the compression limiter is inserted into the bore hole without a scraping action, avoiding potential damage.
Since compression limiters are fabricated wholly in compliance with our customers’ needs, they afford one of the broadest ranges of benefits among fastening solutions.
We arrange the geometry and the material along with you, including outer diameter, inner diameter, material thickness, length, and the installation aids required (e.g. bevels). Almost every geometric shape can be implemented, including round, square, rectangle, oval, and triangle.
Quality, Inspection And Precision
All of Vogelsang’s compression limiters are made to order and designed for high speed automatic feeds. We guarantee 100% optical inspection to ensure that no foreign parts are introduced, so these pins can go from box to vibrating feeder and onto your production line without a problem.
No compression limiter leaves our premises without a 100% check of the dimensions and sorting accuracy.
If you have an existing application in need of a fastening solution, we can work with you to produce the precise part you need. Our team of engineers can also take your project from concept to reality, designing compression limiters right into the application.
When helping you choose or design a compression limiter, we take many considerations into account, including the type of plastics used, corrosion resistance requirements, installation methods, degree of shrinkage, edge spacing, screw size, and more.
Vogelsang compression limiters can hold length tolerance of +/- 0.05mm and replace sintered or cut tube products for substantial cost savings.
Whether molded in place or inserted after injection molding, these cost-effective and customizable fasteners have become an essential component in the manufacturing of automobiles and trucks.
For more information and for help selecting or designing the right part,Ā contact us online or call us at (800) 526-2376 to speak to one of our product representatives. Whatever your needs, we will provide a quality solution to suit your application.